This enables the production of the optical source with the required performance for future high-volume applications, such as co-packaged optics and optical compute interconnect for emerging network-intensive workloads including AI and ML.
The laser array is built on Intel’s 300-millimeter silicon photonics manufacturing process.
Recent co-packaged optics solutions using DWDM technology have shown the promise of increasing bandwidth while significantly reducing the physical size of photonic chips. However, it has been difficult to produce DWDM light sources with uniform wavelength spacing and power.
This development ensures consistent wavelength separation of light sources while maintaining uniform output power, resulting in meeting one of the requirements for optical compute interconnect and DWDM communication
For this research, Intel used advanced lithography to define the waveguide gratings in silicon prior to the III-V wafer bonding process.
This technique resulted in better wavelength uniformity compared to conventional semiconductor lasers manufactured in 3-inch or 4-inch III-V wafer fabs.
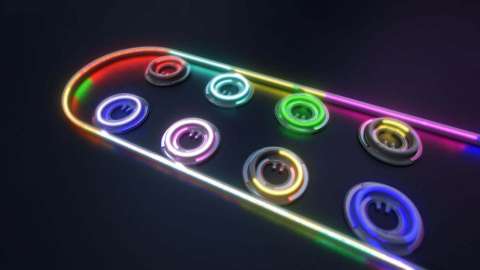
Illustration shows eight micro-ring modulators and optical waveguide. Each micro-ring modulator is tuned to a specific wavelength of light.
The eight-wavelength DFB array was designed and fabricated using Intel’s commercial 300 mm hybrid silicon photonics platform, which is used to manufacture production optical transceivers in volume. This marks a significant advancement in the capabilities of laser manufacturing in a high-volume CMOS fab by utilising the same lithography technology used to manufacture 300 mm silicon wafers.
For this research, Intel used advanced lithography to define the waveguide gratings in silicon prior to the III-V wafer bonding process. This technique resulted in better wavelength uniformity compared to conventional semiconductor lasers manufactured in 3-inch or 4-inch III-V wafer fabs.